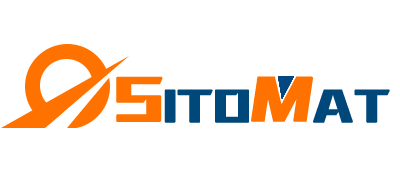
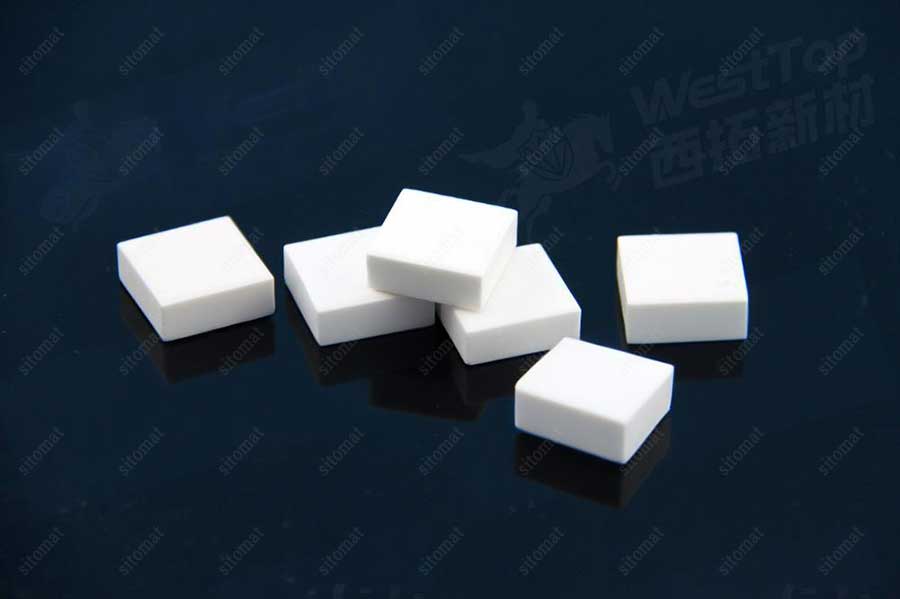
As an industrial wear-resistant material, alumina ceramics have wide application value in industrial fields such as iron and steel metallurgy, cement transportation, machinery manufacturing, new energy batteries and chemical equipment. It is often used as a wear-resistant lining and key structural components of engineering equipment due to its excellent high temperature stability, high wear resistance and electrical insulation performance. The material is based on alumina powder as the basic raw material, which is prepared by molding, high temperature sintering and post-processing. Its density parameters play a decisive role in material properties and performance. It is of great engineering practical significance to systematically explore the key factors affecting the alumina density.
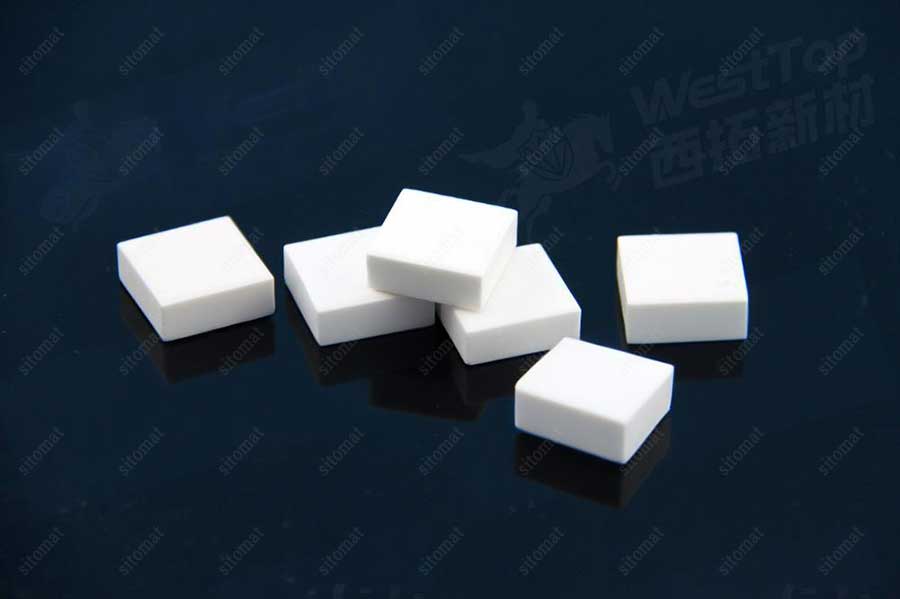
1.Mechanism of forming process
Different molding processes have a significant effect on the microstructure and density formation of alumina ceramics. In the process of dry pressing, the pressure and holding time directly determine the bulk density of the powder, and the internal pores can be reduced by step-by-step pressure combined with vibration-assisted process. Injection molding technology can realize the precision molding of complex structural parts by optimizing the feeding formula ( binder ratio, powder loading ) and injection parameters ( temperature, pressure, speed ), but it is necessary to pay attention to the shrinkage control in the degreasing process. Extrusion molding process requires precise control of screw speed, mold temperature and other parameters to ensure the density uniformity of the extruded body. The research data show that the density variation coefficient ( CV ) of dry pressing products can reach 3 % -5 %, while the CV value can be controlled within 1.5 % by isostatic pressing technology.
2.The importance of process parameter control
Sintering process is the key to determine the final density of alumina ceramics. During the high temperature sintering process at 1600-1800 °C, alumina particles are densified by diffusion and mass transfer. Excessive sintering temperature ( > 1850 °C ) may lead to abnormal grain growth and thermal stress concentration, resulting in cracking. The insufficient sintering time will cause the density to not reach the theoretical value. In addition, atmosphere control ( air, nitrogen, hydrogen ) and cooling rate have an important influence on the phase transformation process. For example, sintering in a reducing atmosphere can inhibit the transformation of α-Al2O3 to γ phase and maintain the stable density of the material. According to the material formulation and product requirements, the operator needs to establish a standardized sintering process curve, and accurately control the temperature change rate ( 0.5-5 °C / min ) and holding time ( 2-6h ) to achieve precise control of ceramic density.
3.Effect of raw material characteristics
The purity and particle size distribution of alumina powder are the internal factors that determine the density of ceramics. High purity alumina raw materials can effectively reduce defects such as pores due to low impurity content, which is conducive to the formation of dense crystal structure during sintering. Studies have shown that for every 0.1 % increase in the purity of alumina, the theoretical density of the material can be increased by 0.5 % -1 %. In terms of particle size, submicron ( 0.5-1μm ) alumina particles can obtain a denser green structure under the isostatic pressing process due to their high specific surface area and good stacking characteristics, and the density is significantly improved after high temperature sintering. In addition, by adding fluxing agents such as titanium dioxide and yttrium oxide, the sintering temperature and final alumina density can be effectively controlled under the premise of ensuring the main performance of the material, so as to adapt to the requirements of different working conditions.
In summary, the density of alumina ceramics is affected by many factors such as molding process, sintering parameters and raw material characteristics. Through the purity control of raw materials, the optimization of molding process and the application of intelligent sintering system, the density of materials can be effectively improved, and then its comprehensive performance can be enhanced. With the integration of material science and intelligent manufacturing technology, the application potential of alumina ceramic tile in high-end fields such as aerospace and semiconductor manufacturing will be further released.