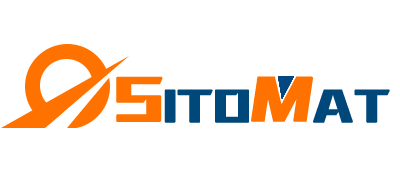
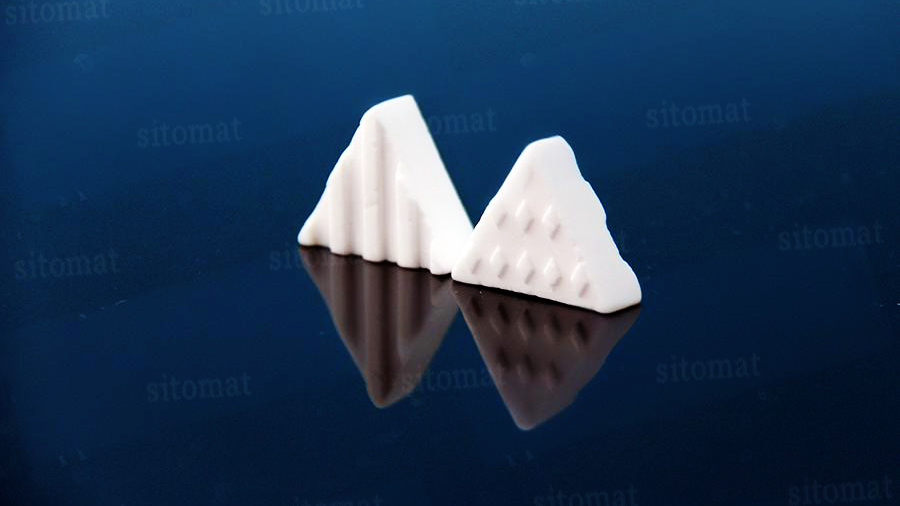
Alumina ceramics are inorganic nonmetallic materials with Al2O3 as the main crystalline phase, and their properties are determined by microstructure and chemical composition. According to the different content of Al2O3, typical products include 92 porcelain (Al2O3≥92%), 95 porcelain (Al2O3≥95%), 99 porcelain (Al2O3≥99%) and other series. As the purity of the main crystal phase increases, the content of impurity phases at grain boundaries (such as SiO2, Na2O, etc.) decreases, and the grain arrangement becomes more dense, thus endowing the material with better mechanical, thermal and electrical properties and meeting the stringent requirements of high-end industrial fields.
I.Microstructure and Properties Correlation The microstructure of the material is composed of the main crystal phase of Al2O3 (α-Al2O3, trigonal system) and the grain boundary phase. When the Al2O3 content increases from 75% to 99%:
Grain characteristics: The average grain size is refined from 5-10μm to 1-3μm, the proportion of grain boundary area is reduced from 20% to less than 5%, the impurity distribution: the glass phase content is reduced from 15% to 1%, the impurity ion concentration of Na and K at the grain boundary is significantly reduced, and the performance is improved: The Vickers hardness is increased from 1500HV to 1900HV, and the high temperature flexural strength (1000℃) is increased from 200MPa to 350MPa. This structure optimization effectively inhibits the intergranular crack propagation, so that the fracture toughness of 99 porcelain (KIC=4.5MPa·m ¹/²) is 50% higher than that of 75 porcelain (KIC=3.0MPa·m¹/²), meeting the extreme working conditions such as high speed cutting and high temperature wear resistance.
II. Key performance parameters
(1) Physical and mechanical properties
Performance Indicators | unit | 92 Alumina | 95 Alumina | 99 Alumina |
Density of alumina | g/cm³ | 3.6-3.7 | 3.8-3.9 | ≥3.90 |
Flexural Strength of Alumina(Room temperature) | MPa | ≥400 | ≥600 | ≥800 |
Young’s modulus alumina | GPa | 300-320 | 340-360 | 380-400 |
Fracture toughness of alumina(KIC) | MPa·m¹/² | 3.0-3.5 | 4.0-4.5 | 4.5-5.0 |
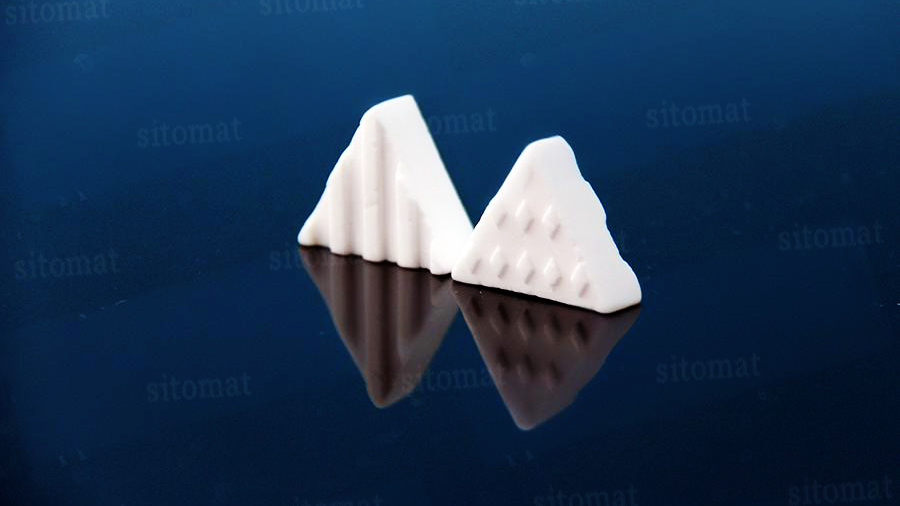
(2) Thermophysical properties
Alumina melting point: 2054℃ (pure Al2O3), the actual sintering temperature increases with the decrease of impurity content (95 Alumina about 1650℃, 99 Alumina ≥1750℃)
Thermal coefficient of expansion of alumina: 7.2×10/K (25-1000℃), significantly lower than steel materials (12×10 Ω/K), suitable for temperature alternating environment.
Alumina heat conductivity: 20-25W/(m·K)(95 porcelain, room temperature), superior to most insulating materials, to meet the heat dissipation requirements of electronic devices.
Alumina use temperature: oxidation atmosphere long-term service temperature ≤1600℃, short-term temperature resistance up to 1800℃
(3)Electrical properties
Alumina volume resistivity: ≥10¹⁴Ω·cm (25℃), 1000℃ still maintain ≥10¹⁰Ω·cm.
Alumina Dielectric constant: 9-10 (1MHz, 25℃), dielectric loss tangent value <0.001, suitable for high frequency circuit applications.
Alumina breakdown strength: ≥20kV/mm, meet the design requirements of high voltage insulation parts.
III.Typical application field
(1) Electronic information field
1. Integrated circuit substrate: high-power LED substrate made of alumina ceramic, using its high thermal conductivity (23W/(m·K)) and low thermal expansion coefficient, solve the problem of too high junction temperature of the chip, and increase the life of the device by 30%
2. Package shell: alumina ceramic is used for IGBT module packaging, and high airtightness is achieved by metallization brazing process.(Leakage rate <1×10⁻⁹mbar·L/s), withstand-55 ℃~150℃ temperature cycle
3. Ceramic capacitor: dielectric constant stability characteristics make it the core material of high-frequency bypass capacitor, the temperature coefficient of capacitance is controlled within ±150ppm/℃
(2) Advanced manufacturing field
1. Precision machining tools: High purity alumina ceramic tools (Hardness HRA≥92) Processing quenched steel (HRC50-60), the cutting speed can reach 2 times that of cemented carbide tools, surface roughness Ra≤0.4μm
2. High temperature bearing parts: In the 1200℃ aeroengine environment, the wear rate of 99 ceramic bearing balls is only 1/2 of silicon nitride ceramics, meeting the high speed (>10⁴rpm) low friction requirements
3. Sealing elements: 95 porcelain seal ring for slurry pump in coal chemical industry, containing solid particles (Hardness>HV1000) In the medium, the life is more than twice that of tungsten carbide seals.
(3) Green chemical industry and energy
1. Corrosion resistant parts: In 20% hydrochloric acid (80℃) environment, the annual corrosion rate of 95 porcelain reactor lining is <0.01mm, far superior to stainless steel.(Annual corrosion rate>0.5mm)
2. Catalytic carrier: alumina ceramic with large pore size (pore diameter 10-20μm) as a catalyst carrier for automobile exhaust purification, the specific surface area reaches 5-10m²/g, improving the adhesion efficiency of noble metal catalyst
3. fuel cell support: alumina ceramic separator in solid oxide fuel cell (SOFC), withstand oxidation and reduction cycle at high temperature of 800℃, interface resistance growth rate <5%/kh
(4) frontier application development
1.Biomedical: Artificial hip joint made of high-purity alumina ceramics (impurity <0.1%), after ISO 10993 biocompatibility test, cytotoxicity grade 0, bone integration rate ≥90%
2.Aerospace: 99 alumina ceramic insulation tile for aerospace engine, in 1500℃ pneumatic heating environment, heat flux density <50kW/m², weight reduction 60% compared with metal parts
V. Technology development trend Current research focuses on:
1.Low temperature sintering technology: The sintering temperature of 95 ceramics is reduced to below 1550℃ by compounding nano-powder (average particle size <100nm) with rare earth additives (such as Y2O3 and La2O3).
2.Structural and functional integration: conductive alumina ceramics are developed (conductivity>10S/cm is achieved by doping TiO2) to meet the requirements of sensor integration. 3. Additive manufacturing applications: alumina ceramic parts with complex structure prepared by SLM technology, with size accuracy up to ±0.1% and porosity <5%.
With the continuous optimization of preparation technology and interdisciplinary application innovation, alumina ceramics are upgrading from traditional industrial materials to high-end functional materials, showing broad application prospects in strategic emerging industries such as integrated circuits, new energy vehicles, and aerospace.